Prototyping
- Fiona Yoon
- Apr 22, 2021
- 3 min read
Updated: Apr 30, 2024
Prototyping is the process of testing ideas and assumptions of a design for validation. Prototypes are built so designers can efficiently develop successful designs, while experimenting and failing in an inexpensive and fast way (1). “By taking the time to prototype our ideas, we avoid costly mistakes such as becoming too complex too early and sticking with a weak idea for too long” – Tim Brown (1).
Designers can prototype during any of the 5 stages: Emphasise, Define, Ideate, Prototype, Test, as prototyping can be used to test out assumptions and ideas, aid a designs development, or test how users may interact with a design (4). Prototyping can be equipped at any stage of a design process, but is usually done at stage 4 when the designer wants to experiment with how the users would interact with their design (1). Designers can produce scaled-down or simpler prototypes to examine the general interaction of users and find faults within its real-life functionality, without putting too much time into the details and large size. By creating simple, smaller prototypes, this saves time and is cost efficient (1). Below is an example of a simplified prototype of a mobile game. This helps the designer understand how users may interact with the buttons and visualises all aspects of the game (2).
Prototyping can improve the accuracy and accelerate the link between the design process and production of the final design. 3D printing, known as ‘rapid prototyping’ is considered to give the most freedom than any other prototyping technique and gives the ability to make multiple iterations quickly (3). 3D printed prototypes are the most accurate, time efficient and an affordable way to test designs as these machines are precise and can vary in materials to test out (3). 3D prototyping helps to spot the small gaps in the structure and materialistic functions of a design (3). By spotting these mistakes and altering the design prior to the production stage, this decreases costly and time consuming mistakes and therefore improves the final product's functionality. Below is an example of a watch design that has used rapid prototyping to accelerate the development and prototyping of the design process (4). As 3D printing is time efficient and inexpensive, the designers were able to test many prototypes of how the watch would feel, move and rest in the arms of the users (4). This picked up the pace of the design process and improved the final designs functionality.
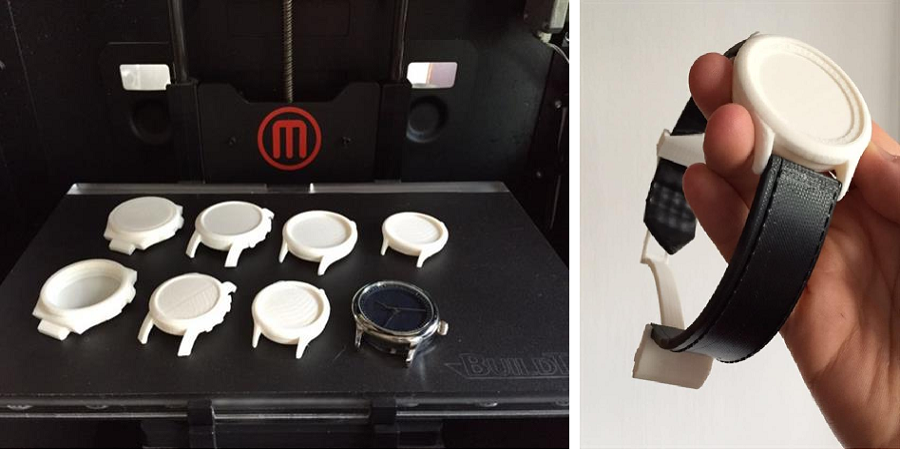
By having more stages of prototyping in my submissions, my final designs functions and impacts could have been improved further and created faster. Prototyping more iterations could have extended my ideas for better solutions, and give a clear visualisation of the practicality of my designs. Real-life scaled prototypes could also help me understand the users interactions of my designs.
-----------------------------------------------------------------------------------------
References
Rikke Friis Dam and Teo Yu Siang. (2020). Stage 4 in the Design Thinking Process: Prototype. https://www.interaction-design.org/literature/article/stage-4-in-the-design-thinking-process-prototype
Felix Leong. (Director). (Dec 27, 2017). Game Paper Prototype - The Secret of the Funfair [YouTube Video]. Felix Leong. https://www.youtube.com/watch?v=dt1bQsZ68iw
Sculpteo. D printing prototypes: How to improve your manufacturing process?. https://www.sculpteo.com/en/3d-learning-hub/3d-printing-business/3d-printing-prototypes/
Rikke Friis Dam and Teo Yu Siang. (January, 2021). 5 Stages in the Design Thinking Process. https://www.interaction-design.org/literature/article/5-stages-in-the-design-thinking-process
Hannah Rose Mendoza. (September 10, 2015). Rapid Prototyping through 3D Printing Lends a Helping Hand to Startup Garibaldi Japanese Selvedge Denim Watches. https://3dprint.com/95087/garibaldi-watches-indiegogo/
Comments